Thesis: Just Glass – Koniari
-
Intro
-
Technical Aspects
Information
Primary software used | ANSYS |
Software version | 2024 R2 |
Course | Thesis: Just Glass – Koniari |
Primary subject | AI & ML |
Secondary subject | Optimization |
Level | Advanced |
Last updated | January 6, 2025 |
Keywords |
Responsible
Teacher | |
Faculty |
Thesis: Just Glass – Koniari 0/1
Thesis: Just Glass – Koniari
Development of a Topology Optimization Algorithm for a Mass-Optimized Cast Glass Component by Anna Maria Koniari
The MSc thesis focuses on the development of an algorithm for the design of large monolithic cast glass structures based on a unified topology optimization (TO) formulation. The algorithm considers both structural (i.e. very low tensile strength of glass, compressive strength, displacement, compliance) and manufacturing limitations (i.e. time-demanding annealing process of glass articles) through efficient material allocation. In this way, it improves considerably the feasibility of such structures which, if constructed, would allow for spatial and light continuity while, at the same time, fully exploit the glass properties, such as its great compressive strength. The thesis continues previous research held by TU Delft MSc students which, although showcased the large potential for the design of these megaliths, underlined the strong limitations that derive from the use of existing mathematical formulations and commercial software as the tool for it.
This is mainly related to the fact that the annealing time constraint and the asymmetric stress failure criteria cannot be captured and, thus, approximations need to be made. Additionally, the constraint evaluation needs to be performed into distinct sequential steps rendering the whole process time-consuming. The customized code was developed following the penalized artificial density method and was applied in a case study example for an interior pedestrian bridge, testing different boundary conditions and glass compositions. The results show that the method converges into robust shapes that comply with all the respective criteria and, therefore, are considered feasible to be manufactured. Upon extraction of the finalized shape, the 3-dimensional geometry is verified structurally using the ANSYS software. Finally, brief guidelines regarding the manufacturing process are discussed.
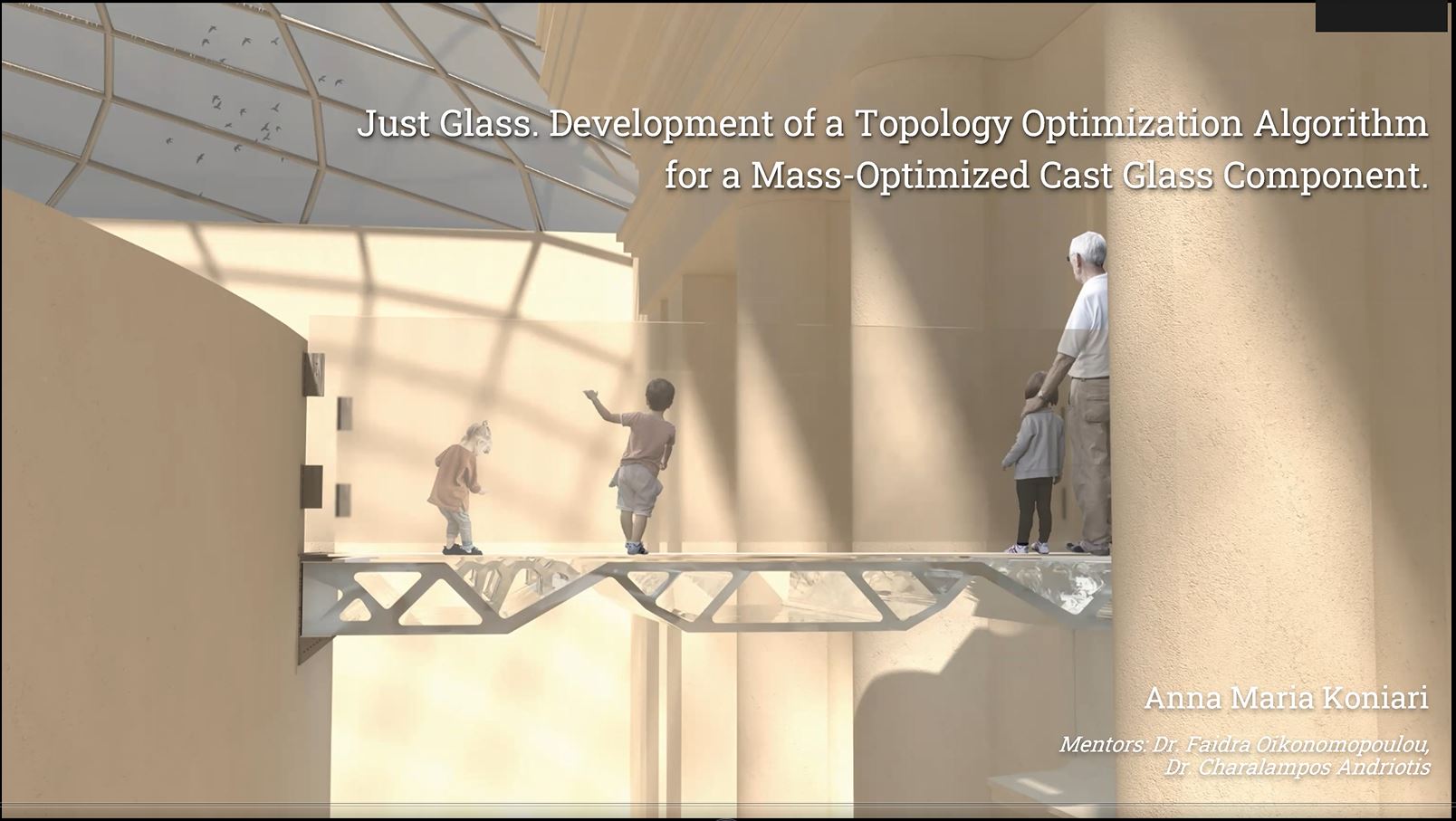
APA: Koniari, A. M. (2022). Just Glass [Master thesis, TU Delft]. https://repository.tudelft.nl/record/uuid:2d1cd8ba-afdb-4d40-9762-abc69db0de52
Here you can find the document of the full master thesis ‘Development of a Topology Optimization Algorithm for a Mass-Optimized Cast Glass Component‘.
Project Information
- Title: Just Glass
- Author(s): Anna Maria Koniari
- Year: 2022
- Link: https://repository.tudelft.nl/record/uuid:2d1cd8ba-afdb-4d40-9762-abc69db0de52
- Project type: Master thesis, Building Technology
- ML Tags: Finite Element Analysis
- Topic tags: Structural Design, Optimization
Thesis: Just Glass – Koniari 1/1
Technical Aspectslink copied
Software & plug-ins used
The customized code was developed in Matlab R2021b. After extraction of the optimized densities, Grasshopper and Rhino were used to translate the densities into a 3d geometry. Finally, ANSYS was used to evaluate the structural integrity of the geometry.
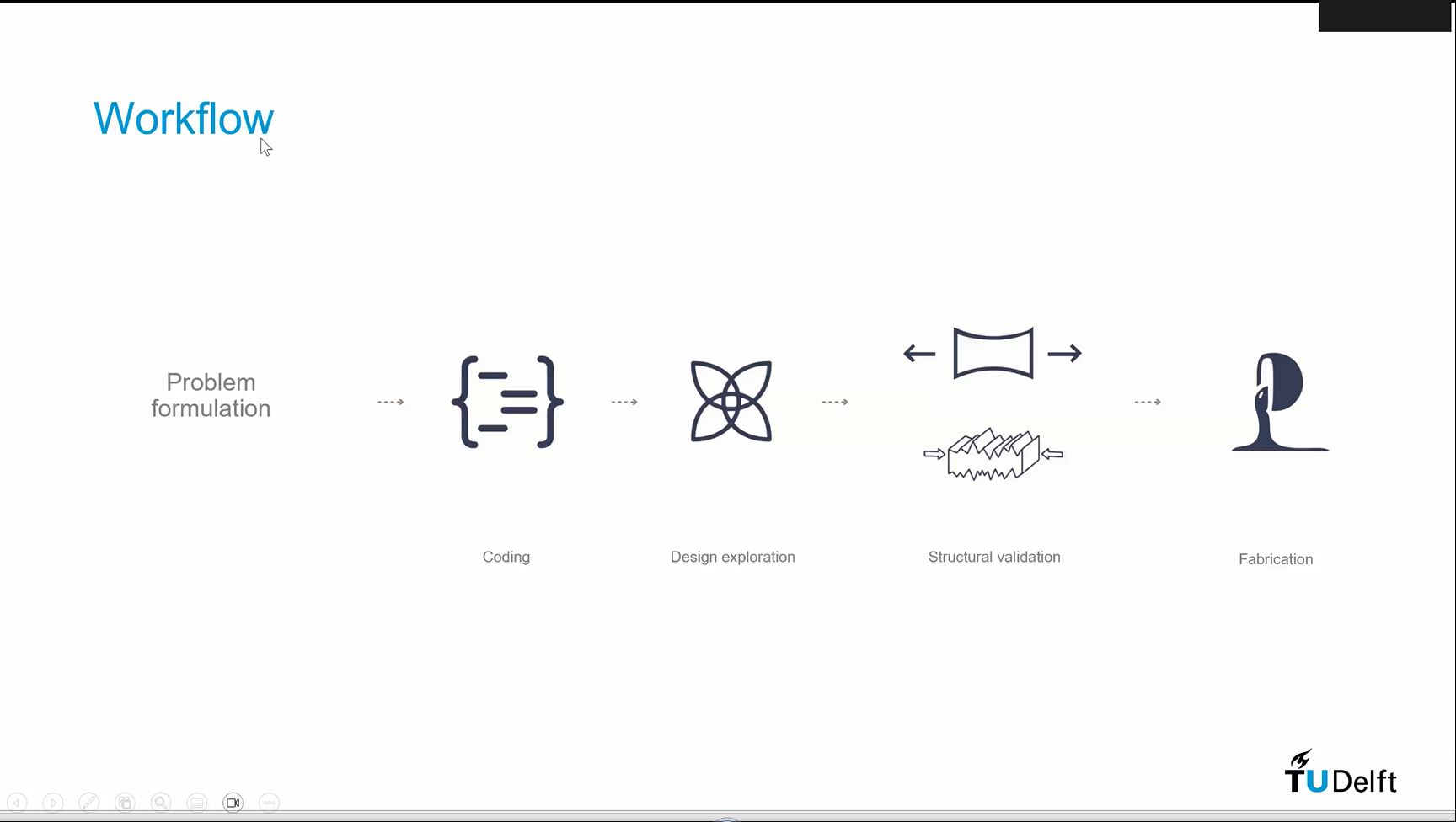
Design Workflow
The approach fits better at the early stage of the design workflow. Given the boundary and load conditions each time, the Topology Optimization algorithm provides an optimal mass distribution that complies with the respective structural and manufacturing criteria. Thus, it can be used as a guide for the designers, providing non-intuitive designs that push the boundaries of the materials. Additional designer preferences can be integrated in the algorithm through modifying the design domain or adding a non-design domain.
ML-Workflow
The customized code was developed following the penalized artificial density method and solved with the interior-point method. The proposed formulation focused on volume minimization of the glass article, while complying with structural (i.e. compliance, displacement, tensile and compressive stress criteria) and manufacturing constraints. Specifically, the latter refers to the maximum imposed annealing time limit, which is translated into a maximum cross-sectional dimension constraint. The maximum value of the cross section is defined through considering primarily the maximum dimension that can be annealed in the set time limit based on the glass composition that is used each time.
The case study refers to an interior pedestrian bridge, whose demand of tensile strength poses an additional challenge to the optimization problem. Specifically, the overall shape, dimensions and boundary conditions are defined based on the needs of an interior bridge placed in the Great Court at the British museum. The total slab is divided along the transversal axis into two identical monolithic components, while laminated float glass sheets cover their upper surface to account for redundancy and safety issues. The algorithm optimizes the characteristic two-dimensional cross section of the individual monolithic components without the top glass sheets.
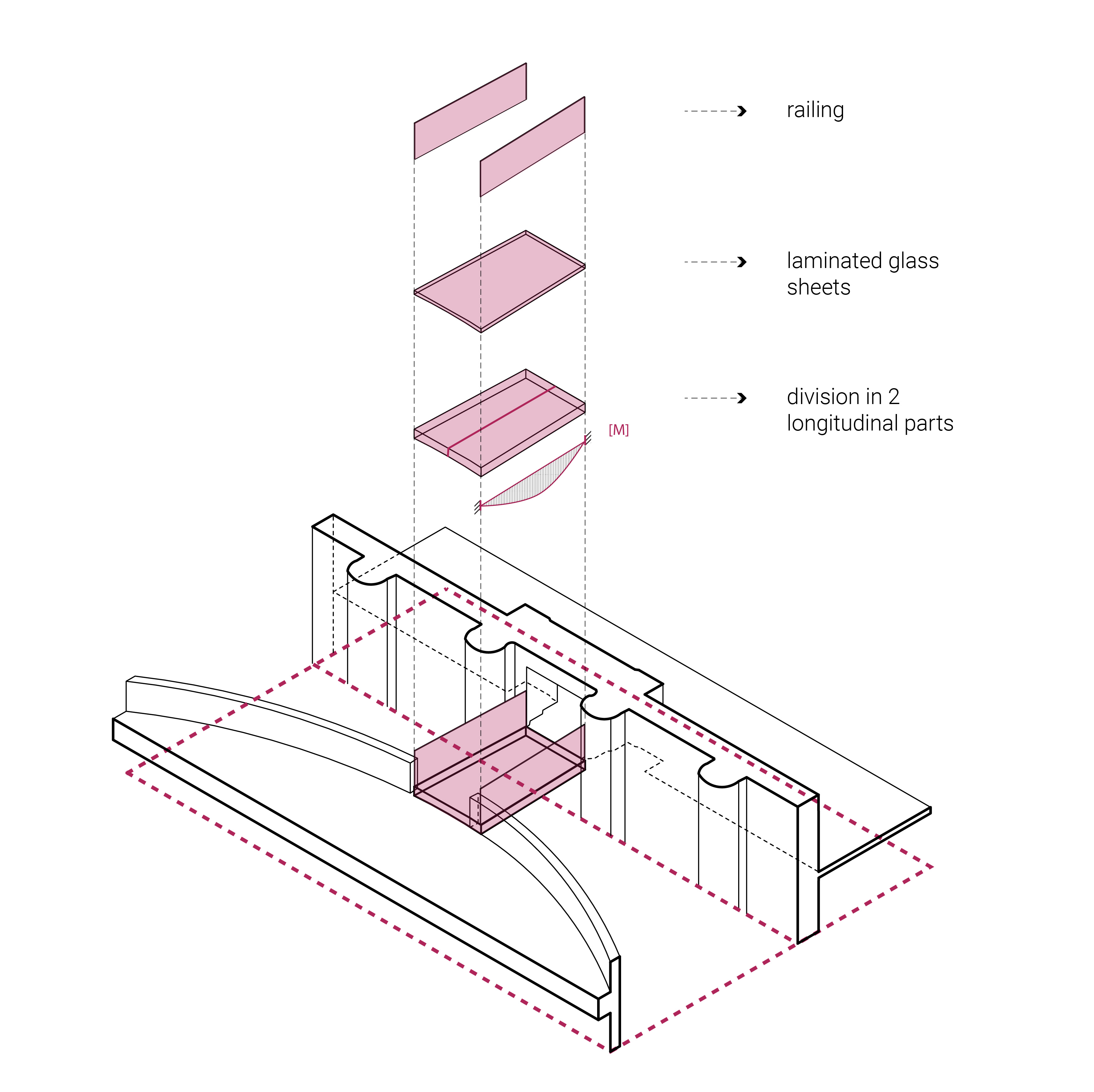
Results based on different glass compositions and structural design strategies were extracted to illustrate the practicality and versatility of the implementation. Regarding the glass composition, the most prevailing two types are applied: borosilicate and soda-lime glass. They share similar mechanical and structural properties, but they have considerably different thermal properties requiring different annealing durations for the same geometry. Particularly, borosilicate glass has significantly lower thermal expansion coefficient, thus cooling down approximately three times faster than soda-lime glass. In all cases, the algorithm converges into robust solutions that comply with all the imposed constraints. Considerably different shapes and volume reduction are achieved based on the glass type and the design strategies applied. Particularly, volume reduction ranges between 10-49% compared to the optimal full-material cross section, i.e. the thinnest slab ensuring sufficient structural performance. Similarly, annealing time is reduced up to 78% compared to the reference optimal slab, ultimately rendering the structures more feasible to manufacture.





The optimization outcome with fixed supports and borosilicate glass composition achieves the largest volume and annealing time reduction while at the same time performs efficiently regarding structural performance. Therefore, it is selected to be applied to the slab design.
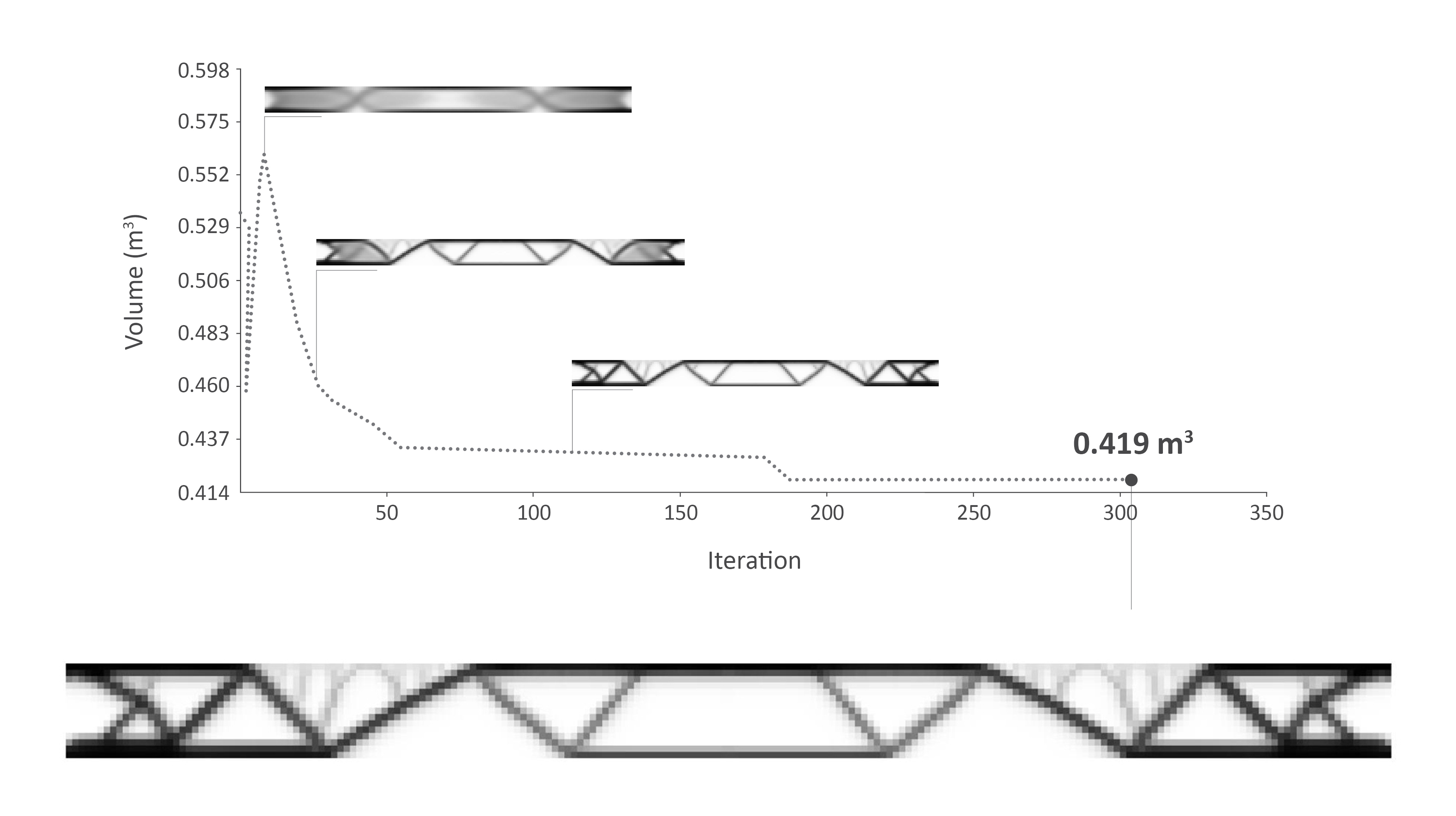
To validate the structural performance of the geometry, the planar optimized cross section is translated into a 3-dimensional shape, through its extrusion along the y axis. The contribution of each design part to the total volume is proportional to its contribution to the structural stiffness during the optimization. Upon extraction of the finalized shape, the 3-dimensional geometry is verified structurally using the ANSYS software.
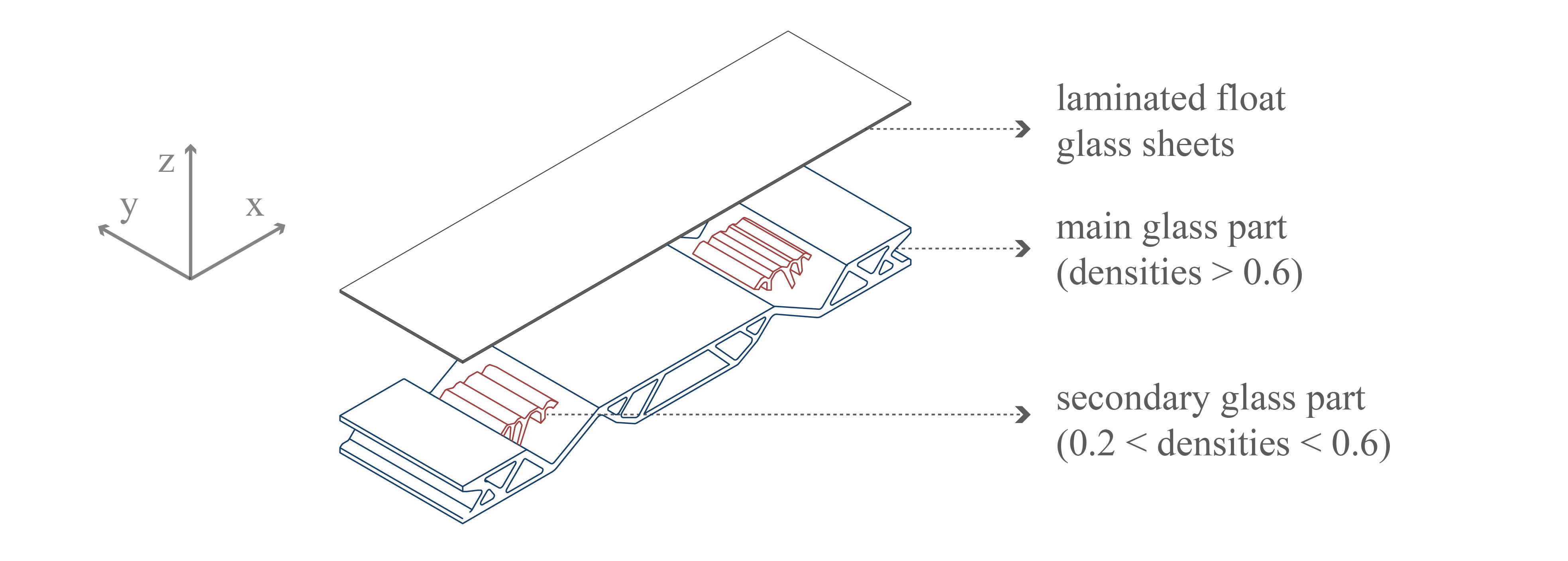
Write your feedback.
Write your feedback on "Thesis: Just Glass – Koniari"".
If you're providing a specific feedback to a part of the chapter, mention which part (text, image, or video) that you have specific feedback for."Thank your for your feedback.
Your feedback has been submitted successfully and is now awaiting review. We appreciate your input and will ensure it aligns with our guidelines before it’s published.